A pivotal step in proving the Additive Casting concept
Enable Manufacturing Ltd has been granted funding from Innovate UK, the UK’s innovation agency, for a project to prove the concept of its Additive Casting process.
Innovate UK, as part of UK Research and Innovation, is investing up to £191 million to fund single and collaborative research and development projects as part of the Sustainable Innovation Fund over the next two years. The aim of these competitions is to help all sectors of the UK rebuild after the effects of COVID-19.
‘In these difficult times we have seen the best of British business innovation. The pandemic is not just a health emergency but one that impacts society and the economy. Enable Manufacturing Ltd and the development of its Additive Casting technology, along with every initiative Innovate UK has supported through this fund, is an important step forward in driving sustainable economic development. Each one is also helping to realise the ambitions of hard-working people.’ – says Innovate UK Executive Chair Dr Ian Campbell.
Under this initiative, Enable has launched a project that is scheduled to run until April 2021 and during which Enable will be designing and producing parts, using all three processes currently available for Additive Casting:
- Sandcasting for large parts (up to 60 tonnes)
- Investment casting for fine detail (up to 250 x 250 x 250mm)
- Investment casting for ultra-fine detail (up to 190 x 160 x 160mm)
The design of the parts will include designs that are optimized for the Additive Casting process as well as designs that cannot be manufactured using traditional manufacturing methods and that must utilize additive manufacturing technology.
Parts will be produced in four different materials including magnesium, which cannot be used in direct 3D metal printing processes due to its highly volatile nature. However, magnesium is a very desirable material in the motorsport industry, for instance, due to its light weight.
The goal of this project is to prove the concept of Additive Casting and to obtain hard evidence that will prove that Additive Casting is currently the only manufacturing method on the market utilizing additive manufacturing technology, that can produce highly complex metal parts, in nearly any size or production volume, in more than 130 materials to existing quality standards applicable to the aerospace, automotive, marine and heavy industries sectors.
‘We strongly believe that Additive Casting is a game-changing technology that will help UK companies innovate quicker, make better quality products and re-shore production for a more sustainable manufacturing model. In this sense, Additive Casting could play an important role in the UK’s recovery post COVID and our journey towards a zero-emission economy. But for us at Enable this grant also means that there are people and organizations who believe in our technology and are prepared to help bring it to market successfully. And for this we want to thank Innovate UK.’ – says Jon Wright, Technical Manager at Enable.
Founded in 2019, Enable specializes in a new manufacturing process for the production of metal parts called Additive Casting, a hybrid process between additive manufacturing and traditional metal casting.
Direct 3D metal printing has not advanced as fast as first expected due to challenges with material properties and choice, quality, and scalability. The Additive Casting process was born out of the desire to benefit from the speed, flexibility and design complexity that became possible with additive manufacturing, whilst still maintaining quality, scalability, and competitive cost structures when producing metal parts. In this process, a mould or pattern for a part is produced with additive manufacturing and then used in the foundry to cast the part in an endless number of metals.
Figure 1: Additive Casting – a hybrid process
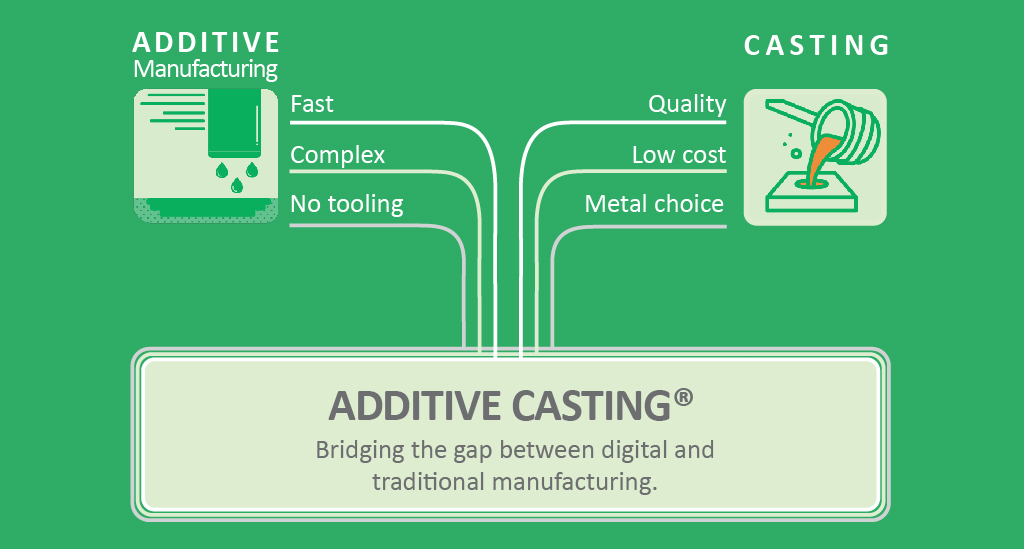
This carves a clear market for Additive Casting and the production of metal parts that are:
- Too complex to be produced with traditional manufacturing
- Too large in size for direct 3D metal printing
- Designed for low to medium volume production, not economical for traditional manufacturing
- Specified for a material not available for direct 3D metal printing
- Designed for certain material properties not achievable by direct 3D metal printing
Figure 2: The Additive Casting market
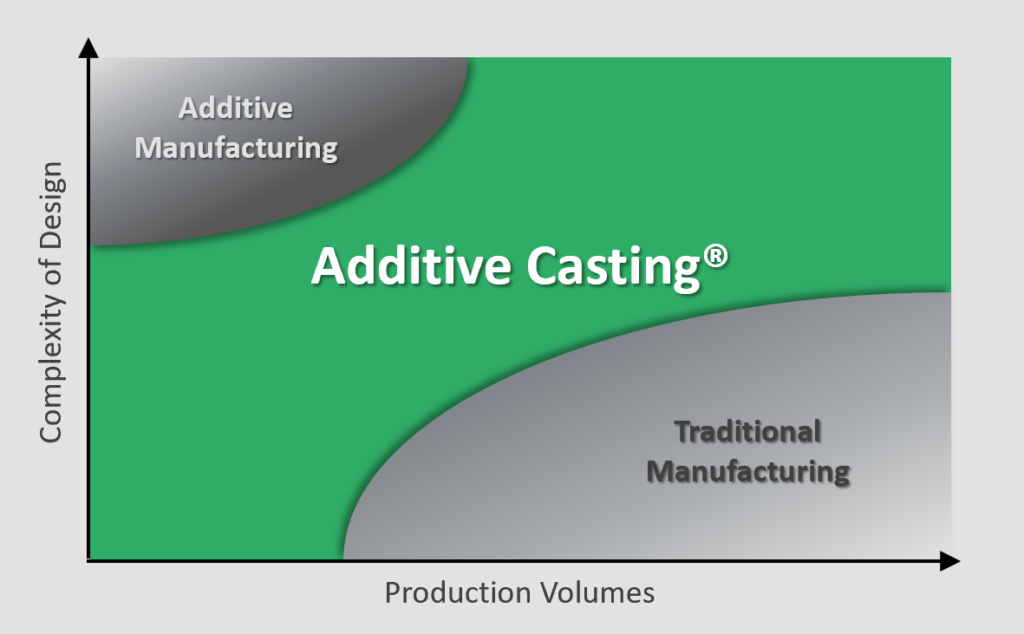
For more information, please visit www.enable.parts.
About Innovate UK, the UK’s innovation agency:
Innovate UK drives productivity and economic growth by supporting businesses to develop and realise the potential of new ideas. Innovate UK connects businesses to the partners, customers and investors that can help them turn ideas into commercially successful products and services and business growth. It funds business and research collaborations to accelerate innovation and drive business investment into R&D. Support is available to businesses across all economic sectors, value chains and UK regions. Innovate UK is part of UK Research and Innovation. For more information visit www.innovateuk.ukri.org
About Enable
Founded in 2019, Enable is a UK based business that specialises in additive manufacturing, including the manufacturing of moulds for metal casting to produce high quality metal production parts without the limitations of traditional tooling. This method is called Additive Casting and bridges the gap between direct 3D metal printing and traditional metal casting. For more information visit www.enable.parts.
For more information, please contact our office:
+44 (0) 3333 05 09 04
office@enable.parts