
Additive Casting®

A Metal 3D printing service with a difference
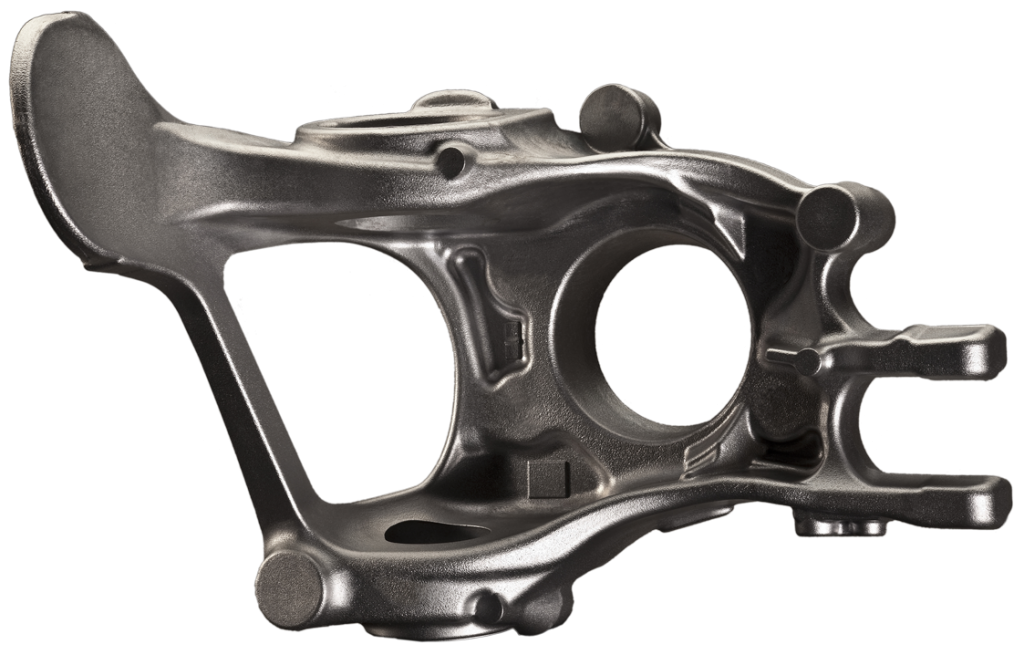
How we make your metal parts
Our Additive Casting® process combines the best of 3D printing and traditional casting to manufacture complex metal parts of any size cost effectively. We use industrial 3D printing to produce moulds and patterns from which we can cast metal parts using nearly any metal. This approach eliminates the need for tooling allowing for more complex parts to be manufactured from your first prototype to your large annual production volume.
We call this Additive Casting:
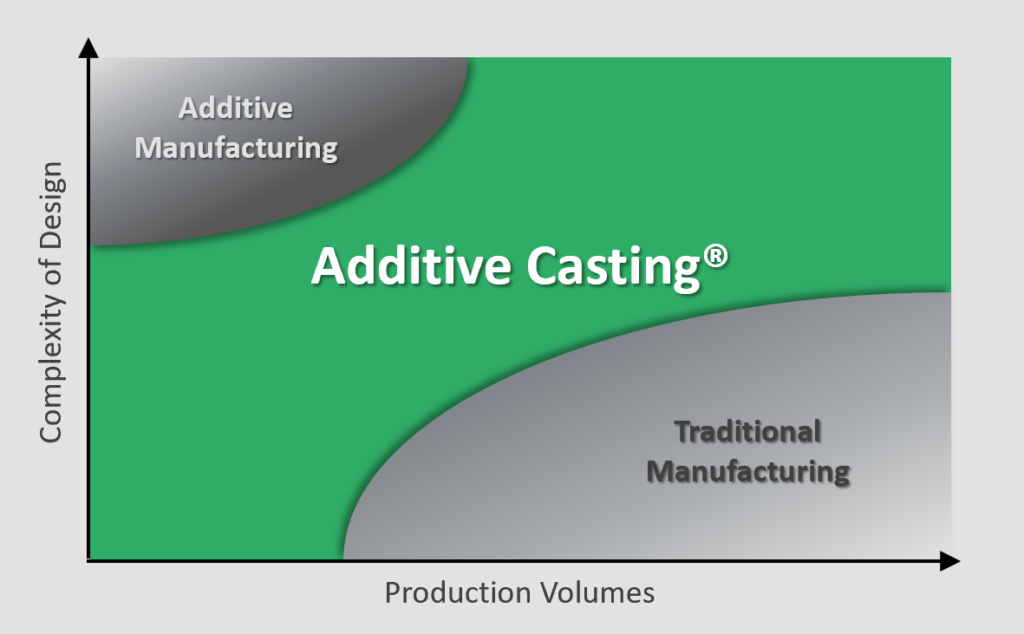
Benefits of Additive Casting
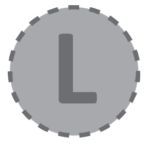
Range of sizes
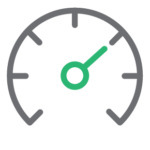
Short lead-times
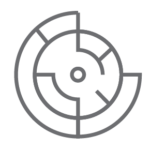
Design flexibility
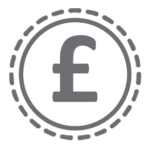
Cost competitive
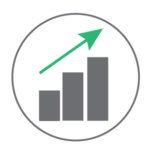
High quality
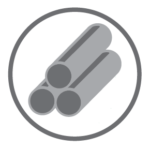
Choice of materials
How it Works
At Enable, we deliver metal parts to you through our Additive Casting process. Click on the buttons below to take a look into the process and how you can order yours today.
Quick Summary
![]() | Upload Your ModelUpload your CAD model(s) to our automatic quotation tool and specify your material, quantity, and any post-processing required. |
![]() | 3D PrintingYour parts are printed on industrial-scale 3D printers as moulds or patterns and prepared for casting. |
![]() | Metal CastingMetal is poured into the 3D printed mould or pattern and allowed to cool before post-processing. |
![]() | DeliveryYour parts are thoroughly inspected before being packaged and shipped directly to you. |
Detailed Description
![]() | Upload Your ModelUpload your CAD models to our instant quotation tool. Specify your material, quantity, and optional post-processing. Depending on part complexity, choice of metal, quantity, or post-production requirements, we may opt for our manual quotation to ensure you receive the most accurate price possible. |
![]() | File PreparationWe take your CAD models and prepare them for 3D printing and casting. Checking each file for defects and turn your file into either an investment casting pattern or a sand mould before efficiently nesting your parts without compromising the final part quality. |
![]() | 3D PrintingYour parts are printed on industrial-scale binder jet 3D printers as moulds or patterns and are unpacked, depowdered, and waxed (Investment casting only) to prepare them for casting. Quality control and inspection is carried out at all these stages to ensure the 3D printed parts meet your standards. |
![]() | Metal CastingFor thin walled, highly detailed parts, your printed parts are first coated in a ceramic shell before being burnt out, leaving a hollow shell which metal can be poured into. For larger parts sand moulds are used. The process is much simpler, allowing us to pour metal straight into the negative impression. |
![]() | Post-Production & InspectionOnce the metal has cooled down, the ceramic shell or sand mould is broken away revealing your metal parts. These are shot-blasted to improve the surface quality before proceeding to optional post-production and final inspection. |
![]() | DeliveryOnce inspection is complete and your parts have passed all quality control checks, we package and ship them directly to you. |
Three Unique Processes
Sand
Additive Casting
This process is ideal for very large and heavy parts, and suitable for rapid prototyping and production volumes up to 100,000 per year.
Investment
Additive Casting
This process is particularly suitable for rapid prototypes and medium production volumes of complex parts.
Vacuum
Additive Casting
This process is particularly suitable for small and highly intricate parts and suitable for rapid prototypes or volumes up to 100,000 per year.
Parts made with Additive Casting
Design credits
Mask: Steamtowers, May 09, 2018. Minor changes were made for the manufacturing process.
Coin: kwallnation, March 13, 2016. Minor changes were made for the manufacturing process.
Lattice: Gen3D
About us
Who we are
Enable is a UK business that first started in 2019 with the vision to bring a new, innovative manufacturing process to life that we call additive casting. In this process, we specialise in additive manufacturing of moulds for metal casting to produce high quality metal production parts without the limitations of traditional tooling.
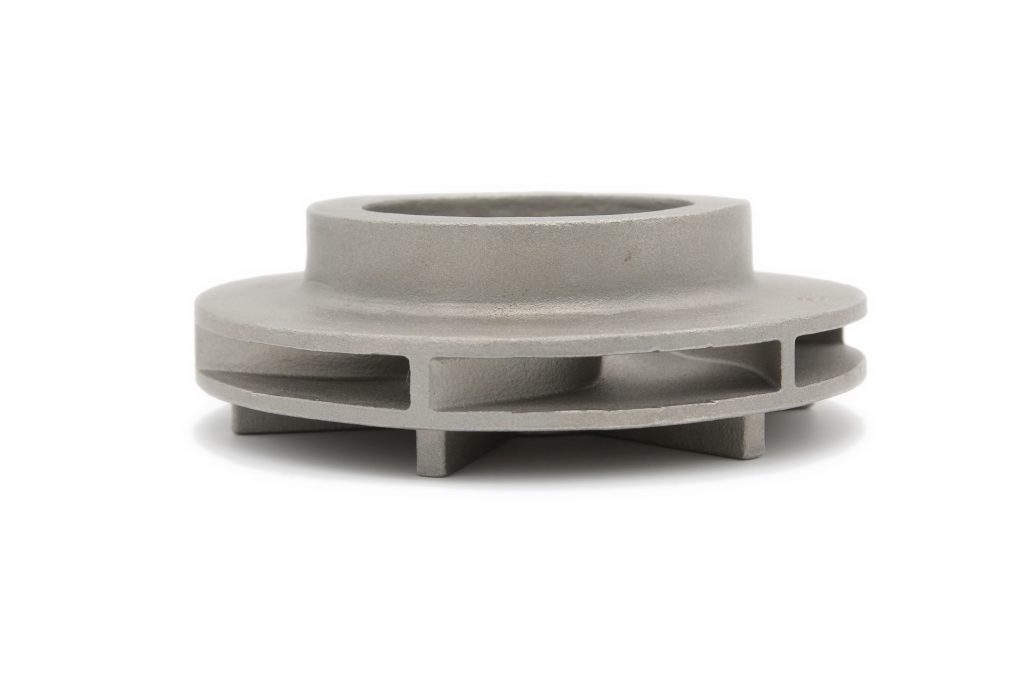
Enable People
The team at Enable offers over 35 years of 3D printing experience, extensive knowledge about material capabilities for certain industries and a large supply chain network. All of this allows us to offer a full manufacturing service to our clients with complete peace of mind.